How digital twins achieve deeper engineering insights
Within the facilities management industry, we’re always talking about how to achieve more, such as:
- Improved energy efficiency
- Higher cost savings
- Better services
And at the root of that drive for more, there’s a foundational need for insight.
In this series of articles, we’ve already covered how important data is for engineering, and how analysis has enabled the shift from reactive to proactive and predictive maintenance. But now it’s time to talk about the next level of insight – a way facilities managers can use the data streams across their estates to make more informed decisions about maintenance, engineering and upgrades. So let’s talk about digital twins.
Digital twins: real-time insight
A digital twin is a virtual environment that precisely replicates a physical environment within your estate. That digital twin could be linked to anything from an office block to a production line, and at any scale, from a single asset to an entire facility. Any part of your estate that can be fitted with sensors can be replicated as a digital twin.
Digital twins vary widely in scope and application – there’s no one-size approach to this. One organisation may choose to create a twin of its core manufacturing equipment in order to pick the right moment to carry out maintenance and avoid disruptive downtime. Another might choose to model its data centre, and test radical redesigns of racks and climate control systems. On the broadest scale, leadership may benefit from a digital twin that spans the entire organisation. This is what’s most exciting about the technology; there’s so much value to be derived from digital twins, and so many opportunities to right-size the application for whatever project is at hand.
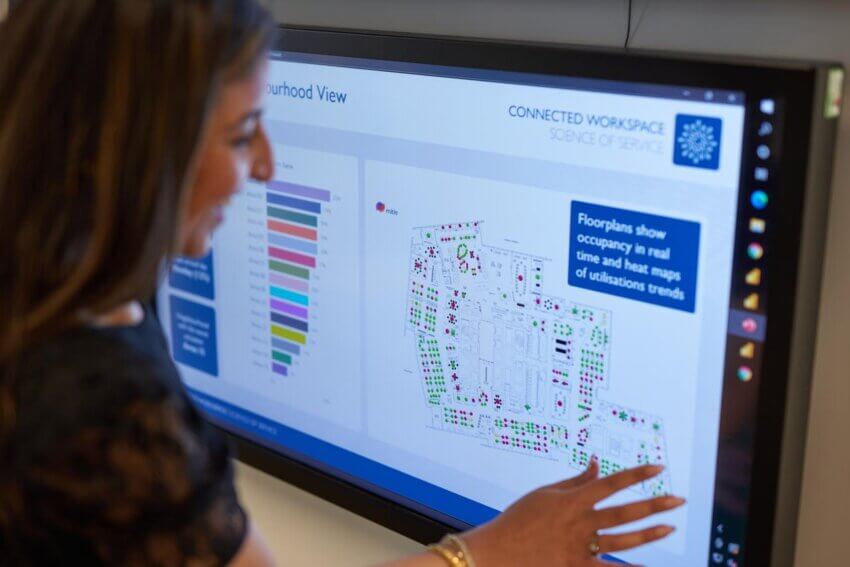
Digital twins are an excellent option for organisations that have an especially large footprint, or facilities in far-flung areas. Some of our clients have buildings in the highlands of Scotland. These are ideal candidates for digital twins. Instead of sending technicians out regularly to manually observe the site’s physical condition, managers have all the information they need at their fingertips. It’s visualised in the digital twin so they can understand if an unusual reading from a sensor is a one-off anomaly, or something that could affect vital systems. The time savings make this a more efficient approach, which also avoids the carbon emissions associated with travelling to site. So, while establishing and maintaining digital twins can be energy-intense, this can be offset thanks to the efficiencies they make possible.
Go beyond today with digital twin simulation
These real-time streams of information give a detailed overview of performance, efficiency and areas that need attention from engineers, technicians and maintenance teams. They also provide all the data you need to ask, “What if?”
That’s because a digital twin doesn’t just offer insight into what’s happening right now; it also provides a sandbox where you can model potential outcomes for your maintenance, engineering and upgrade strategy. So, if you’re wondering how a major refurbishment could reduce your estate’s energy efficiency, you can alter your digital twin to see the effect before you begin the revamp.
For example, one Mitie client used its digital twin to model whether applying solar film on its windows would keep offices cooler during summer for better comfort and energy efficiency. Our analysis uncovered an unexpected downside: the effect was year-round. So, workers were likely to need more heating in the winter – effectively wiping out their cost and energy savings from reduced air conditioning use in the summer. The client made an informed decision not to proceed with the solar film.
Think about the long term – while maintaining flexibility
In the world of estate management things can change quickly. And in some organisations, leaders are always looking for ways to reimagine their estate in order to:
- Build more appealing spaces
- Squeeze more value out of assets
- Support people to be more productive
That means many facilities managers are forced to think relatively short term – a few years ahead at the most, so they can stay agile.
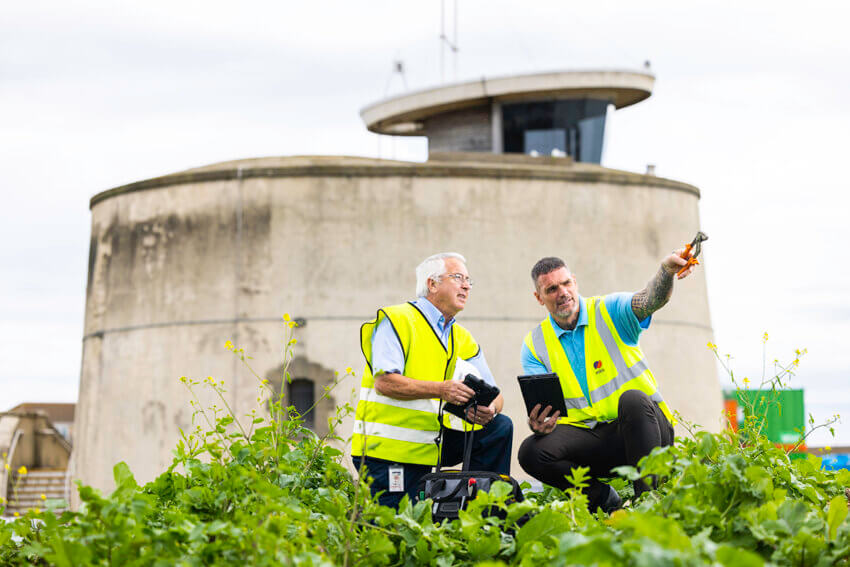
But while this outlook gives them flexibility, it can sometimes prevent them from making truly strategic choices. They’re unable to plan ahead for an asset’s full lifecycle and beyond to make sure they’re getting the most value from their investments.
The insights from a digital twin are constantly refreshing, drawing information from as many sources as you can feed into it. And that means you can make small changes to your strategy to adapt to your situation week to week, while also making provisions for your estate’s long-term future.
Complex technologies, straightforward outcomes
While the challenges may change over time, they’re fundamentally rooted in the same goals. A digital twin delivers the fast-moving advantage of adaptation while allowing you to think strategically about how you can best use your engineering and maintenance resources. You can use its insights and simulations to maximise the lifespan of your assets while designing, building and maintaining the most practical spaces for your organisation.
In facilities management, success is all about finding the simplest, most effective solution to a challenge. Swap out a component to extend an asset’s lifespan; match your maintenance schedule to the company’s hybrid working patterns; switch an office’s light fixtures over to more energy-efficient alternatives.
In a complex estate, a lot of work can go into finding these simple answers. At Mitie, we work alongside clients to identify whether a digital twin is right for their organisation. They are available alongside other cutting-edge technologies including IoT sensors, remote monitoring, building information modelling (BIM), artificial intelligence (AI) and data analytics.
We make it easy for you to find the insights you need, so you can be confident that every choice you make about your engineering strategy is the right one – whether you’re making a decision about today, or five years in the future.
If you’re interested in learning more about how a digital twin might fit into your engineering and maintenance strategy, visit mitie.com/engineering.
Read next
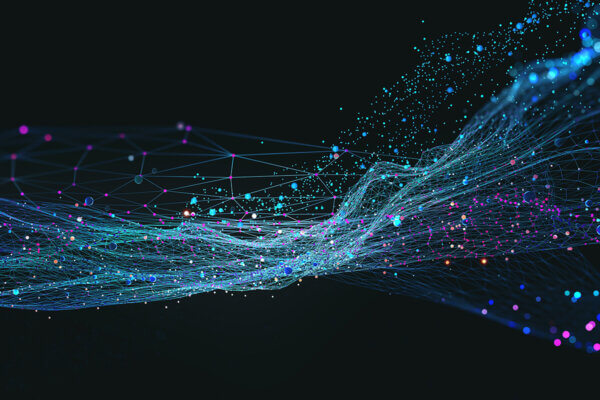
Accurate data: the foundation of good AI for facilities management
AI can be an invaluable tool to help facilities managers get the most from their estates. But to be truly useful, it needs to be fed with accurate and meaningful data. By Dan Blake…
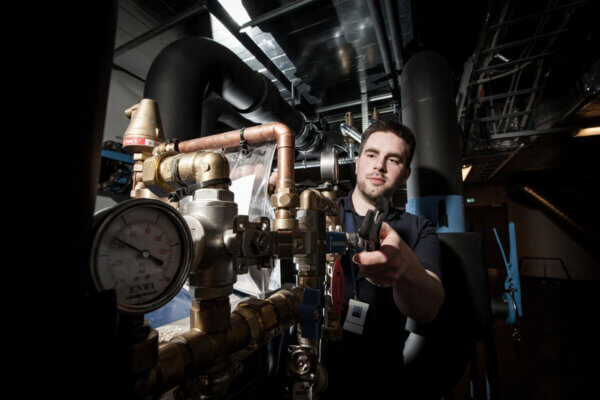
Predictive and preventative: the most crucial words in maintenance
What’s your biggest engineering and technical services challenge? Where do faults and failures crop up the most? The modern estate can be incredibly complex to manage. For plenty of organisations, there are gleaming, new…
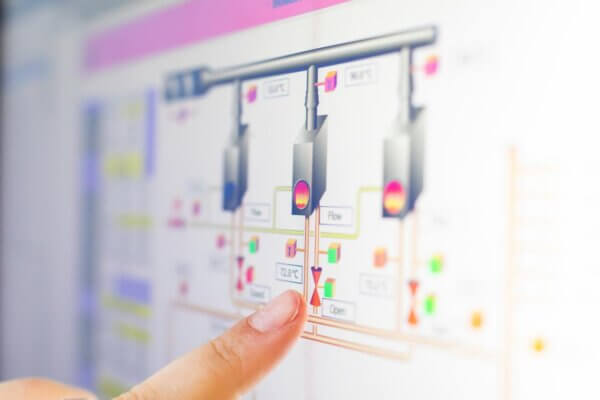
Supercharge your engineering strategy with data and AI
Ever thought that a deeper understanding of your facilities and assets would transform your organisation’s engineering and technical services? You’re not alone. It’s the eternal challenge – the need to find new efficiencies, operate…